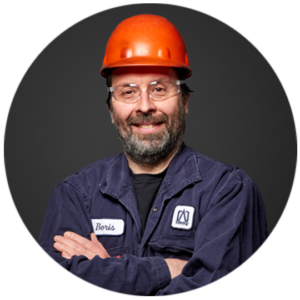
From a young age, Boris had an interest in the Electrical trade. He grew up around manufacturing and had the opportunity to attend a specialized school focused on training Electricians.
His interest in TMMC was sparked when he heard about the strong learning and development opportunities available. He joined TMMC and is going strong on 10 years of employment. Learn more about what Boris values about his role and how he’s taken advantage of the TMMC training.
What aspects of your current role do you specifically value or appreciate the most?
I really like the work environment. The level of automation and the speed of production, it keeps me interested and involved every day. I get the chance to work on new technology; including PLCs, automated guided vehicles (AGV) and robots. This gives me the opportunity to continue to learn and develop my skills.
What is a skill you learned since being at TMMC?
Before working at TMMC I had zero experience with robotics. At my last employer, we had 1 robot, and I didn’t get a chance to work on it. When I joined TMMC in the Weld shop, there were more than 600 robots. Over the last 9 years, I have been satisfied with my achievements as a maintenance team member. Thanks to TMMC’s training program, I’ve developed not just my technical skills, but a range of skills that allows me to perform my work at my best level.
Do you perform work that is different or beyond what an Electrician would typically do?
Yes, at TMMC we work in a multi-skilled environment. This means my daily troubleshooting may include broken metal that needs welding or a pneumatic hose that needs to be replaced. Most of the preventative maintenance checks and adjustments are not related to the Electrical trade. I see this as a benefit as I get continued exposure to activities outside of my trade. This makes me a better professional.
What do you want most from your career?
I want my day to feel fulfilling.
I find this at TMMC. I have had a chance to be involved with many kaizen circles and projects, and I have had the opportunity to work with team members from Production and other employment groups. We share ideas and work together to find a solution. This allows me to continue to focus on improving the production process.
After a project is implemented, we check the results to see if further improvements can be made.